Good Manufacturing Practice (GMP)
Good Manufacturing Practice (GMP) constitutes an essential component within sectors such as pharmaceuticals, food production, cosmetics, and medical devices. It comprises a comprehensive array of guidelines aimed at ensuring that products are consistently manufactured and regulated in accordance with established quality standards. GMP is instrumental in protecting public health, fostering consumer confidence, and guaranteeing adherence to regulatory requirements. This article delves into the most recent developments, foundational principles, and applications of GMP across diverse industries.
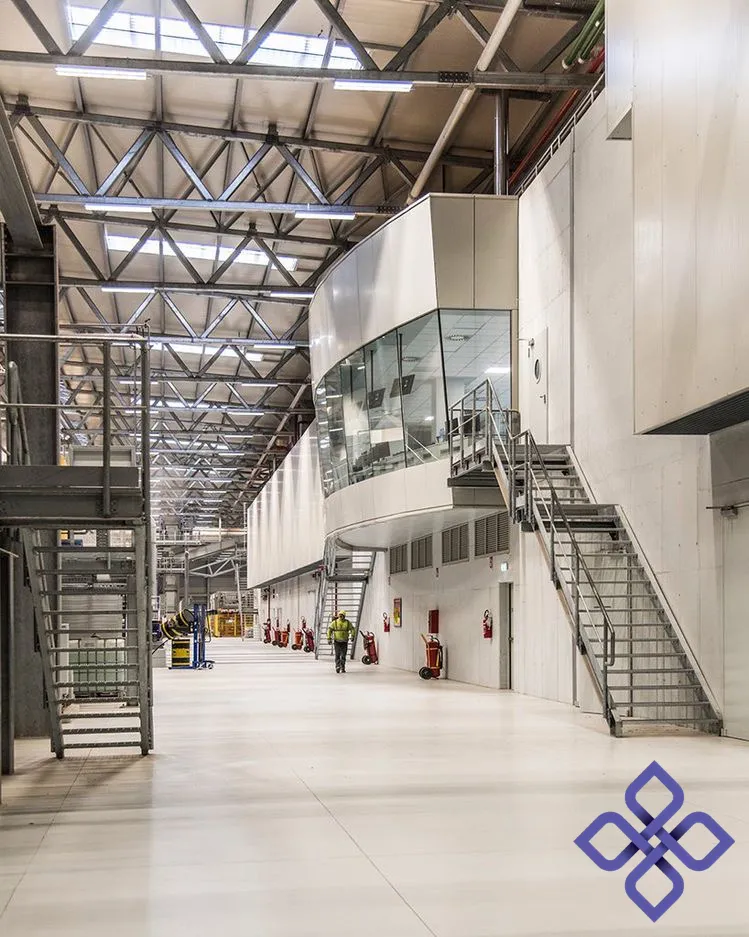
Goharshid Nesfeh Jahan Ali Qapu Company provides a comprehensive suite of services for food industry professionals, drawing on a consulting team of both academic and industry specialists. Our offerings include guidance on the design and construction of food processing facilities that meet GMP standards, sourcing and importing production equipment from Europe, product formulation, and support in acquiring necessary permits from relevant authorities
What is GMP?
GMP, denoting Good Manufacturing Practice, pertains to the systematic approaches that guarantee products are produced and managed to conform to quality standards. These practices encompass all facets of production, including the sourcing of raw materials, facility management, equipment functionality, and personnel training. Adhering to GMP significantly mitigates risks that cannot be wholly addressed through post-production testing
Core Principles of GMP
1. Quality Management
Defined Processes: Establishing transparent and validated processes to ensure uniformity. Documentation: Maintaining thorough records to facilitate traceability throughout each phase of the production process
2. Personnel and Training
Employees are required to undergo comprehensive training and possess a thorough understanding of GMP protocols.
Regular updates and competency evaluations are essential to uphold ongoing compliance
3. Premises and Equipment
Design and Maintenance: Facilities should be architected to reduce the likelihood of contamination. Equipment Calibration: Scheduled maintenance and calibration must occur to guarantee precision
4. Raw Materials and Supplies
Only materials sourced from approved suppliers and certified for quality should be utilized.
Rigorous quality assessments are necessary to avert adulteration
5. Production and Process Controls
Monitoring of critical parameters such as temperature, humidity, and pH levels is mandatory.
Ensuring the traceability of batches and materials utilized is imperative
6. Quality Assurance and Audits
Conducting regular internal and external audits is vital for evaluating compliance.
Continuous improvement efforts should be initiated based on the findings from audits
GMP in Different Industries
1. Pharmaceutical Industry
Focus Areas: Emphasis on sterility and contamination prevention. Accurate labeling and appropriate packaging practices
Recent Updates: The incorporation of artificial intelligence for quality monitoring and predictive analytics for batch optimization.
2. Food Industry
Key Principles: Mitigation of cross-contamination risks between raw and processed food items. Ensuring optimal storage conditions to maintain freshness and safety.
New Trends: The integration of blockchain technology for enhanced traceability. A heightened focus on allergen management.
3. Cosmetics Industry
Requirements: Conducting safety testing to assess skin compatibility. Ensuring hygienic conditions throughout the production process. Emerging Practices: Utilization of sustainable and clean-label ingredients. Enhanced transparency in sourcing of ingredients.
Recent Updates in GMP Standards
Annex Revisions: Updates to European Union GMP Annexes to reflect technological advancements. Digitalization: The transition to electronic records and batch monitoring systems
Harmonization: Collaborative efforts to standardize GMP practices on a global scale, including alignment with WHO, FDA, and EMA guidelines
Focus on Sustainability: Integration of environmentally sustainable practices within manufacturing processes
Benefits of Adhering to GMP
- Assurance of Product Quality: Builds trust in the safety and effectiveness of products among consumers.
- Legal Adherence: Prevents potential legal issues and product recalls through compliance.
- Enhanced Productivity: Minimizes waste and maximizes the use of resources in operations.
- Access to New Markets: Eases the process of entering markets with strict regulations
Challenges in GMP Implementation
- Financial Burden: Significant upfront costs associated with compliance infrastructure and employee training.
- Regulatory Complexity: Challenges in understanding and meeting varying regulations across different regions.
- Integration of Technology: The need to adapt to emerging digital tools and technological advancements
Future of GMP
- Utilization of Data Analytics: Employing big data to improve predictive quality management.
- Implementation of AI: Using artificial intelligence and machine learning to refine process management and decision-making.
- Commitment to Eco-Friendly Practices: Adopting sustainable manufacturing methods.
- Harmonization of Standards: Efforts towards aligning GMP regulations globally
Conclusion
In summary, Good Manufacturing Practice is essential for maintaining product quality and safety in regulated sectors. By adopting modern standards, cutting-edge technologies, and environmentally friendly practices, manufacturers can achieve compliance while meeting the changing demands of consumers and regulatory authorities. The ongoing evolution of GMP will continue to play a crucial role in public health and the integrity of the industry
